Differential Gear Less Conversion System (DGL)
At Smart Tex Automation, we’re unwavering in our commitment to revolutionize the spinning industry through cutting-edge machine conversion services.
Let’s Start Work
Together
Please feel free to contact us. We will get back to you with 1-2 business days. Or just call us now.
+91 99441 99123 |+91 98949 83174
SMART TEX AUTOMATION S.F.No.15, Barani Nagar, Thirumalai Garden, Subramaniyam Palayam, Gounder Mills, Coimbatore - 641029.
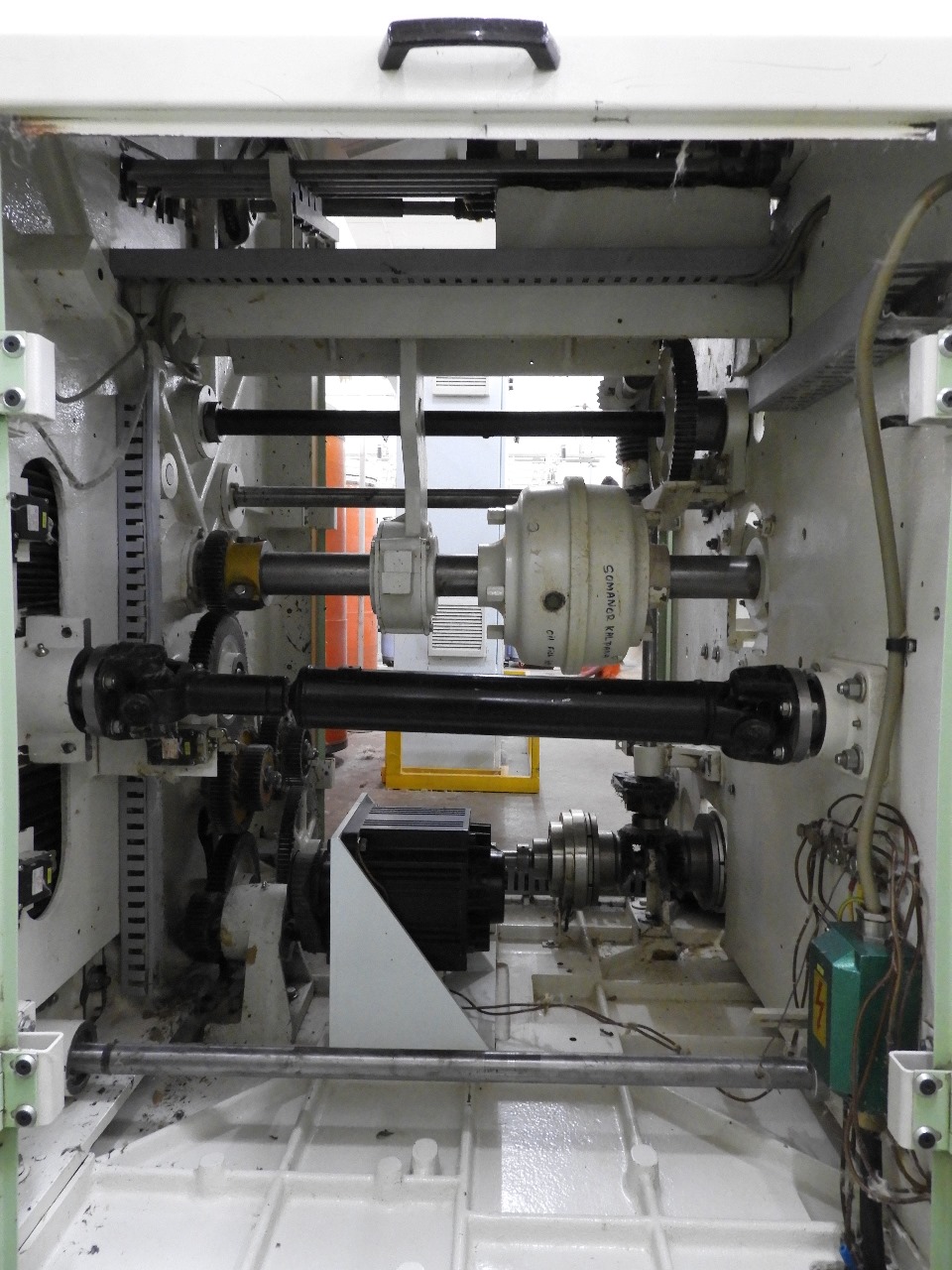
Differential Gear Less Conversion System (DGL)
At Smart Tex Automation, we’re unwavering in our commitment to revolutionize the spinning industry through cutting-edge machine conversion services. Building upon the success of our Roving Automation Conversion (RAC), we introduce the Differential Gear Less Conversion (DGLC). With decades of industry expertise and a relentless pursuit of excellence, we’ve taken the RAC concept to new heights, offering a transformative solution that redefines efficiency, precision, and sustainability in the textile world.
Taking RAC to the Next Level for Unprecedented Efficiency
Our Differential Gear Less Conversion (DGLC) is the evolution of the RAC conversion, delivering a host of advanced features that elevate your spinning mill to new horizons
Comprehensive Assessment
We initiate the DGLC process with a meticulous assessment of your existing RAC enhanced machines, ensuring a seamless transition to the next level of efficiency.
Customized DGLC Plan
Based on our assessment, we craft a tailored DGLC plan designed to maximize the potential of your machines, all while incorporating the latest innovations.
Differential Drive System
The heart of the DGLC conversion is the integration of a state-of-the-art differential drive system. This groundbreaking technology optimizes yarn handling with unparalleled precision.
Features
- Production improvement.
- Quality improvement and consistent stretch%.
- Maintenance free.
- No need for a Pneumatic system.
- Sliro Master Elimination (Optional).
- On/Off/Inch triple push button (Optional).
Flexibility
- Production improvement upto 10% from the existing production.
- Bobbin content can be increased upto 10%.
- Maximum flyer speed can be reached to 1300 rpm.
- Roving slough off issues can be avoided.
- Bobbin rail can be manually operated without effort.
- Bobbin rail direction can be changed at doff restart.
- Maintenance and maintenance costs free as the Cone drums, Gear box, Builder motion unit, Soft start unit, Electro-magnetic clutch unit, T-Plate setup, Pneumatic system and Belt shifting unit were removed.
Automation
- Main motor will be replaced with a 7.5kW motor.
- High-quality Servo is used instead of mechanical cop building mechanisms.
- A 2.2kW motor is used for the bobbin rail.
Reduced Maintenance
The upgraded components are built for durability and reliability, translating into significantly reduced maintenance requirements and minimized downtime.
Real-Time Machine Control
The differential drive system enables real-time control of yarn tension, twist, and handling, granting you precise process management capabilities.
Seamless Machine Interface
We integrate modern operator interfaces, including touch displays, to enhance user experience and ensure effortless machine interfacing.
Competitive Edge
The DGLC conversion gives your spinning mill a competitive edge that’s unmatched in the industry. You can adapt swiftly to market dynamics and customer demands.
Regulatory Compliance
Our conversions adhere to the latest industry regulations and safety standards, ensuring that your operations remain at the forefront of compliance and safety.
Comprehensive Training
Our team provides comprehensive training to your staff, enabling them to operate and maintain the upgraded DGLC – enhanced machines with expertise.
Long-Term Investment
The Differential Gear Less Conversion (DGLC) is a strategic long-term investment that promises enduring benefits, including increased productivity, substantial energy savings, and unmatched yarn quality.
With the Differential Gear Less Conversion (DGLC), we invite you to step into the future of spinning mill efficiency, precision, and sustainability—a future where your operations set the industry standard.